Selecting the proper hardware is crucial in a piezo haptic solution. The solution is composed of a piezo actuator and a piezo haptic driver (amplifier). Both are deeply connected and rely on each other to deliver the best tactile feedback. Therefore, selecting the right components is very important to achieve the best possible results.
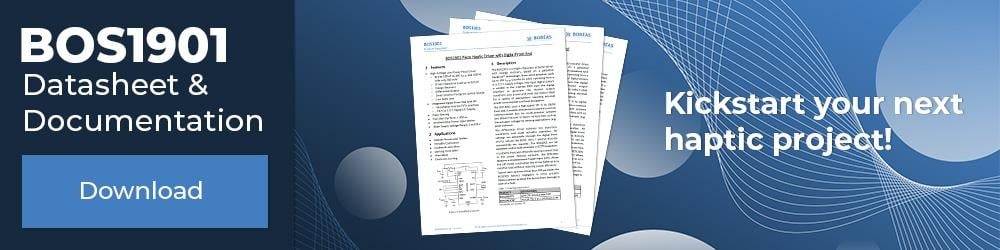
To help you select the perfect combination, we will see what technical specifications are relevant to look for when choosing the components in your piezo haptic solution. This decision will involve many people from your team: product designers, mechanical engineers, and electrical engineers will help you analyze and select the appropriate piezo haptic components. Let’s start with the first step, choosing the proper piezo actuator for your application.
Selecting the Proper Piezo Haptic Actuator
The product you are designing will significantly impact which piezo haptic actuator and driver combination you can use. There are multiple factors to consider because integrating piezo haptics in a smartphone will substantially differ from adding haptics to an automotive display. You need to be able to answer four questions to select the best actuator:
- What’s the mass you are trying to move?
- How much volume or space is available?
- What is the power source?
- Do you need force sensing in your product?
1. Mass
The first thing to consider before selecting your piezo components is the force requirement. The feedback strength is based on Isaac Newton’s laws of motion. You can learn more about the mechanical fundamentals of piezo haptic actuators here.
Newton’s second law of motion tells us the sum of the forces F on an object is equal to the mass m of that object multiplied by the acceleration a of the object: F = ma. (It is assumed here that the mass m is constant)
The piezo actuator’s job is to generate acceleration. It’s the engine of your haptic solution. What you need to determine is the mass you are trying to move. If your mass is small, like replacing a button in a smartphone, you can achieve high acceleration with a lower force (N). On the contrary, if you try to move a large and heavy automotive infotainment system, you’ll need a higher force (N) actuator to achieve the same acceleration and tactile feedback.
When considering a specific actuator, moving a higher mass will limit the maximum achievable acceleration.
2. Volume
The second thing you need to determine before selecting your piezo actuator is the actual volume you have available to fit the component in your product design. Piezo actuators often have different shapes and can create force in different axes.
You need to know how much space you can use to fit the actuator and determine which axis you'll use to create the desired vibration.
This will again depend on your application and the type of tactile effect you are trying to achieve. You may have to update your design according to the piezo actuator to integrate it, so it's best to have a good idea from the start of what type of piezo actuator you will end up using.
3. Power Source
Another critical aspect to consider before selecting your piezo haptics component is the power source of your product. Piezo haptics requires high voltage to work. This is why you need a piezo driver; it controls the actuator and amplifies the necessary high voltage from the power source. Therefore, you need to be aware of your power source to ensure it will provide enough power to feed the piezo driver. A mobile device battery doesn’t offer the same power levels as an automotive alternator, for example. Piezo drivers are designed within those parameters, and they might not work on every power source. You need to select your components accordingly.
4. Force Sensing
Thanks to the reversible piezoelectric effect, piezo actuators can also be used as force sensors. Piezo material generates an electric charge when they are deformed. Applications where feedback is triggered by user input, like button replacement, can make great use of this feature.
You now have all the relevant information to select the best piezo actuator! You can now select a suitable piezo driver to complete your haptic solution. Please keep in mind that it is essential to have the actuator’s technical requirements not too far; they will help you select your driver.
Selecting the Right Piezo Haptic Driver
Your piezo actuator will lead your driver selection. The two main tasks of your piezo driver are to amplify the voltage of your power source and control the actuator. Therefore, your actuator technical specifications are essential to select the best piezo driver. The relevant actuator technical specifications you need to choose your piezo driver are the required output voltage, polarity, capacitive load, and output bandwidth.
1. Voltage
The piezoelectric effect is the interaction between the mechanical and electrical potential in crystalline materials. Applying voltage through a piezoelectric material changes the crystals' electric polarization and creates mechanical deformation (the material can expand or shrink).
TDK PowerHapTM 0904H014V060 elongation measured between cymbal end-caps as a function of voltage. Source: 0904H014V060 Datasheet
The piezo actuator’s mechanical movement is the result of the applied electric field through the material. Therefore, it is essential to respect the minimum voltage requirements for your piezo driver. Using less than the required voltage will result in less material movement and less feedback from the actuator.
TDK PowerHapTM 0904H014V060 force-stroke diagram with different load springs. Typical stiffness 150 N/mm. Source: 0904H014V060 Datasheet
2. Polarity
Talking of the material polarity, you need to be careful when you select your piezo driver. Some actuators will be bipolar, meaning they can sustain waveforms with both positive and negative amplitudes, and some are unipolar, meaning they can only work with positive voltage waveforms.
Our BOS1901 piezo driver is bipolar; it can drive 190 volts peak-to-peak (+ 95 and – 95 V).
You need to be aware of your actuator polarity to select a piezo driver that can effectively work. Generally, a bipolar driver will drive a unipolar piezo actuator, but the opposite is not valid.
3. Capacitive Load
Piezo actuators have inherent capacitance, meaning they electrically behave like a capacitor. Typically ranging from a few nF to a few µF for haptic piezo actuators, the capacitance determines the amount of energy required to create a voltage that will induce enough strain in the piezoelectric material to create a vibration.
A higher capacitive load will require higher power to charge it quickly, making sure your piezo driver supports the actuator capacitance.
4. Output Frequency Bandwidth
TDK PowerHapTM 0904H014V060 acceleration peak-peak as a function of frequency for different loads. Source: 0904H014V060 Datasheet
Frequency plays a significant role in haptics quality for three reasons:
- A higher frequency generally equals a higher acceleration and a stronger perceived effect for a given sense receptor.
- Our somatosensory system (touch sense) uses different receptors depending on the vibration’s frequency. Depending on the type of tactile effect you are trying to achieve, you need to be sure to use the appropriate frequency range for the proper touch receptor.
- The natural resonance frequency of the mass you are trying to move. The natural resonance is the frequency at which the mass resonates when it is vibrating, meaning the mass displacement is amplified to its maximum. Typically, a lower mass increases the natural frequency, while a higher mass reduces it. This concept is essential for applications desiring to maximize the effect of continuous vibrations.
Piezo actuators have a wide frequency bandwidth, meaning they can vibrate over a continuous frequency range. You need a piezo driver that can provide the maximum required frequency for the actuator capacitance and maximum voltage to achieve its highest acceleration performance.
5. Power Consumption
While power consumption isn't related to the actuator's feedback quality, it is still a significant factor when choosing a piezo driver. High-power consumption will drain your device battery and generate excessive heat that may limit functionality or even be a hazard for the system.
Not all piezo drivers are power-efficient. Previous piezo driver technologies used inefficient architectures to amplify voltage and generate high-voltage waveforms. They were power hogs. Boréas Technologies CapDriveTM technology architecture is different. It recovers the energy from the actuator's internal capacitance and reuses it instead of draining all the battery power. It allows our drivers to use less than one-tenth of the power of other piezo drivers on the market and avoid any overheating issues.
Bonus: CapDriveTM Exclusive Force Sensing Feature
Another advantage of our CapDriveTM technology is the driver’s ability to sense the pressure applied to the piezo actuator. Since the piezo effect is reversible, it means that the actuator generates an electric voltage when mechanical stress is applied to it. CapDriveTM drivers can detect this voltage change and allow a single IC to be used for sensing and haptic feedback functions. It means, depending on your application and actuator integration, that you may be able to replace the complete sensing hardware with your haptic solution.
Leave a comment